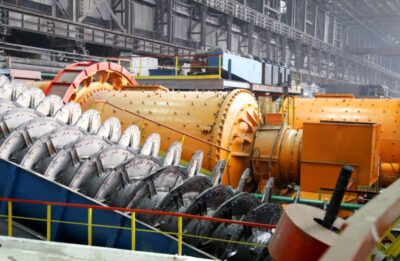
Il est bien connu que toutes les exploitations minières sont confrontées à un problème majeur qui affecte non seulement le fonctionnement de l’usine, mais aussi et surtout les résultats financiers, à savoir l’abrasion. Depuis le moment où le minerai commence à être transporté par une méthode quelconque vers l’usine de traitement, jusqu’à l’endroit où le produit final est manipulé, des équipements critiques sont affectés par l’abrasion. Dans certaines régions, l’équipement d’exploitation peut nécessiter une réparation ou un remplacement en l’espace d’une semaine seulement, en raison de l’environnement d’exploitation agressif des usines minières.
Avant de décider comment protéger les équipements contre l’usure par abrasion, il est important d’identifier les différents types de mécanismes abrasifs, qui ont tous pour effet d’affecter et d’user les surfaces des équipements :
Meulage sous contrainte
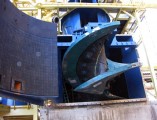
- Ce phénomène se produit généralement lorsque deux surfaces opposées sont en mouvement relatif et que des particules se trouvent entre elles. Si une force est appliquée sur les particules, il en résulte une réduction de la taille mais aussi une perte à la surface de l’une ou des deux surfaces opposées.
- Ce type de contrainte qui associe abrasion et contrainte mécanique, est généralement observé dans les équipements tels que les concasseurs et les broyeurs. La perte de métal dans ces équipements vitaux de l’usine affecte directement le rendement et la production.
Abrasion par glissement à faible contrainte
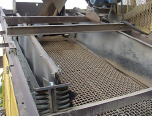
- Dans ce type d’abrasion, il y a généralement une surface statique sur laquelle des particules glissent parallèlement. Ce processus affecte la surface en la « rayant », ce qui modifie son épaisseur.
- Ce type de mécanisme d’usure affecte généralement les équipements qui gèrent le mouvement des boues et d’autres équipements où les particules se déplacent sur la surface. Les équipements concernés sont les pompes à boues, les goulottes, les agitateurs et les cyclones.
Gougeage Impact-Abrasion
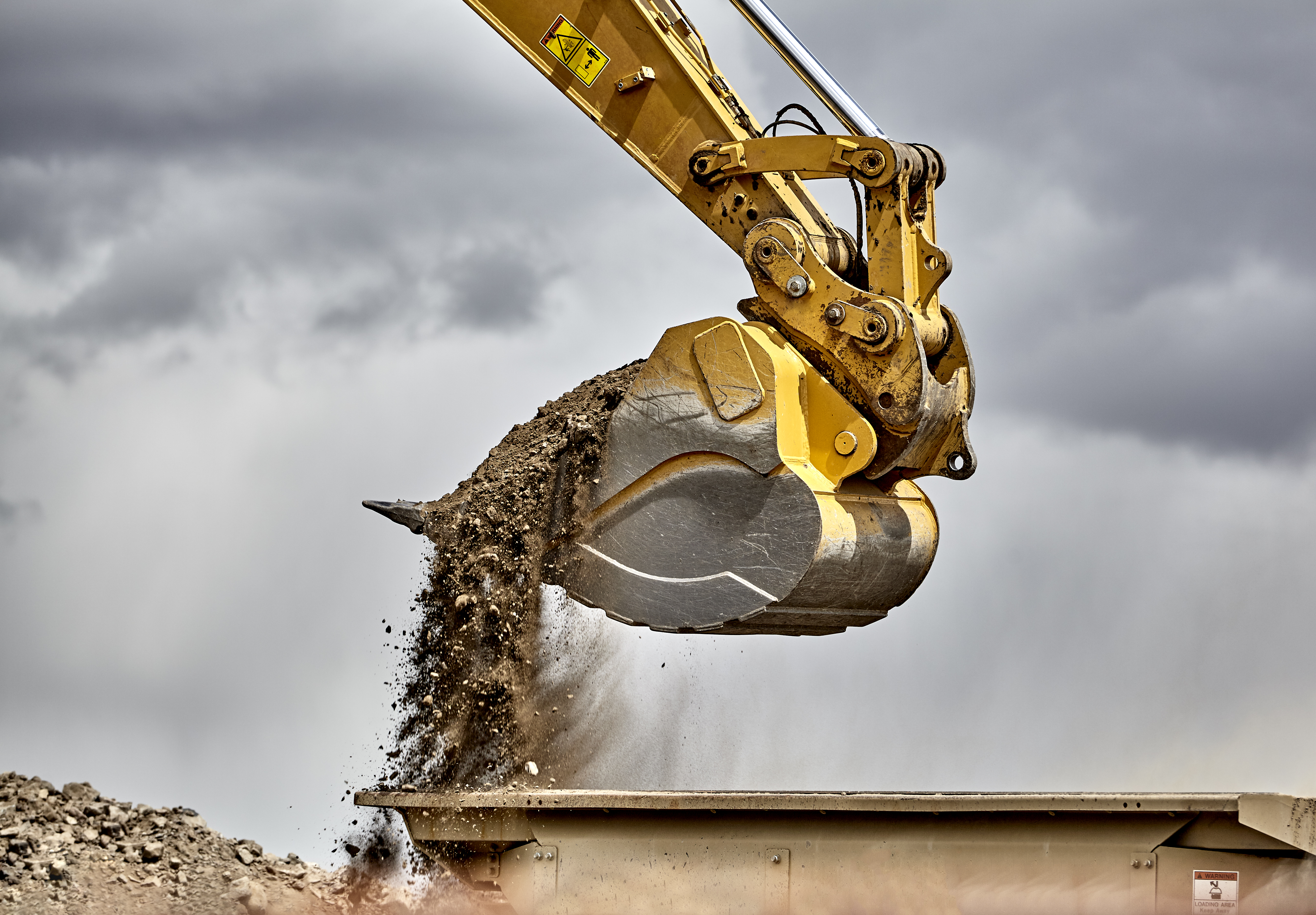
- Ce type d’abrasion est observé lorsqu’un flux de particules ne glisse pas parallèlement à une surface, mais à un angle élevé, et que les particules impactent la surface en formant des « piqûres » dues à l’effet de gougeage des particules sur la surface.
- Avec le temps, les substrats métalliques peuvent se déformer plastiquement et entraîner une défaillance de type fatigue. Ce mécanisme est couramment observé sur des équipements tels que les godets des lignes de traîne, les excavateurs et les concasseurs.
L’agressivité et la sévérité d’un processus d’abrasion dans les situations décrites précédemment sont influencées par les facteurs suivants :
- Dureté des particules : plus les particules sont dures, plus le mécanisme d’abrasion est sévère.
- Forme des particules : les particules de forme irrégulière entraînent une abrasion plus agressive que les particules arrondies.
- Densité des particules : affecte particulièrement l’abrasion par impact : plus la densité est élevée, plus l’énergie est importante impact dans une surface.
- Taille et poids des particules : les particules plus grosses ou plus lourdes entraînent des taux de perte de métal plus élevés.
- Vitesse des particules : une vitesse plus élevée des particules augmente le taux d’abrasion.
- Différence de dureté entre les particules et les surfaces d’usure : les particules plus dures produisent plus d’abrasion.
- Force d’impact : généralement directement proportionnelle à la hauteur des particules tombant sur une surface d’usure.
- Pourcentage de particules solides dans la boue : plus le pourcentage de solides est élevé, plus la boue est abrasive.
- Débit massique : plus le débit est élevé, plus le niveau d’abrasion augmente.
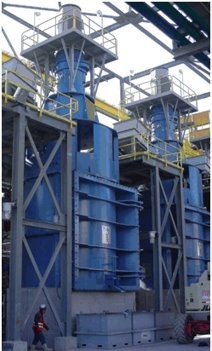
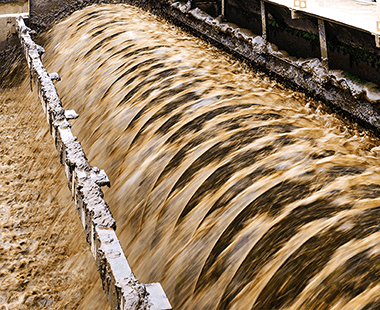
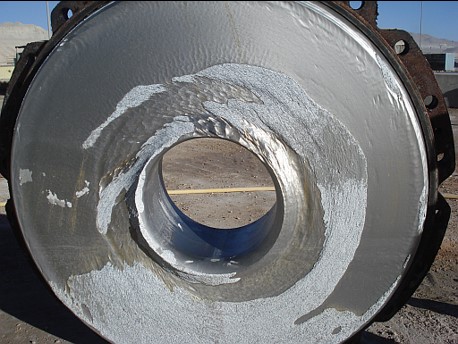
Avantages pour les clients de l’utilisation de revêtements renforcés de céramique
Au cours des 30 à 35 dernières années, les technologies de revêtements renforcés par des céramiques ont été introduites sur le marché industriel, les industries minières et de traitement des minerais reconnaissant de plus en plus les avantages potentiels de l’utilisation de ces technologies pour la protection contre l’abrasion de l’équipement d’exploitation critique.
Quels sont exactement ces avantages et quels sont les avantages qu’ils présentent par rapport aux matériaux traditionnels et même aux nouvelles technologies de protection contre l’abrasion ? Analysons la situation :
- Comme indiqué précédemment , l’abrasion est l’un des principaux facteurs qui influent sur la production dans les exploitations minières. Le montant des investissements consacrés quotidiennement à la réparation/remplacement des équipements usés représente une part importante du budget total de maintenance d’une exploitation minière.
- Le temps d’arrêt de la production est un autre facteur extrêmement important. Les arrêts imprévus de certains équipements de production dans les grandes mines peuvent entraîner des pertes de production de 50 000 euros par heure, voire plus.
- Disponibilité de l’équipement : ce point est directement lié aux coûts d’immobilisation, car chaque fois qu’une pièce d’équipement doit être réparée, elle doit être arrêtée ; par conséquent, l’industrie est toujours à la recherche de solutions plus durables.
- La facilité de mise en œuvre de la solution influe également sur le temps d’immobilisation de l’équipement, car plus il faut de temps pour mettre en œuvre une solution résistante à l’abrasion, plus la perte de production est importante.
En prenant en considération les facteurs clés décrits, nous pouvons les mettre en relation avec les avantages que les revêtements céramiques offrent à cette industrie :
- Ils constituent la solution la plus rentable pour résister aux conditions d’abrasion, si l’on compare le coût du revêtement au temps d’immobilisation de l’équipement et à la durée de la solution.
- Facile à appliquer, il peut être appliqué dans un atelier ou directement là où se trouve l’équipement, ce qui permet également de réduire les pertes de temps d’arrêt .
- Ils s’adaptent facilement à toutes les formes de surface et à toutes les géométries d’équipement.
- Ils peuvent être utilisés pour réparer les technologies traditionnelles et nouvelles de protection contre l’abrasion, telles que les revêtements en caoutchouc ou les carreaux de céramique, ce qui permet de gagner du temps par rapport à l’enlèvement de grandes surfaces de revêtements ou de revêtements existants.
- Ils ont fait la preuve de leur performance et durent plus longtemps que le caoutchouc, les alliages spéciaux et les carreaux de céramique, même en cas d’impact.
- Peut être facilement réparé, ce qui signifie que le revêtement restant après une période de fonctionnement n’a pas besoin d’être enlevé mais seulement nettoyé pour accepter le nouveau revêtement.
- Ils peuvent très bien adhérer à différents types de substrats, tels que tous les types de métaux, le caoutchouc, les carreaux de céramique et les revêtements similaires renforcés de céramique, après une préparation adéquate de la surface.
- Ils peuvent réduire le stock de pièces de rechange, puisque de nombreuses pièces peuvent désormais être réparées une fois et une autre, tant que elles sont structurellement saines.
- Ils sont appliqués sans qu’il soit nécessaire de travailler à chaud, ce qui améliore la sécurité mais signifie également que tout substrat métallique ne se fatigue pas en raison de la chaleur activée par le stress.
Ces avantages expliquent pourquoi l’industrie minière et de traitement des minerais utilise des revêtements renforcés de céramique pour réparer, protéger et recouvrir les équipements exposés à des conditions abrasives.
Applications courantes
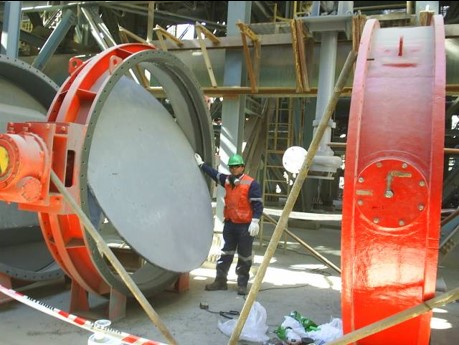
Ces revêtements renforcés de céramique sont principalement utilisés pour protéger les équipements soumis à l’abrasion par glissement sur deux corps ou en cas de détérioration de l’équipement due à un impact. Ils peuvent également être utilisés pour protéger des équipements soumis à la corrosion chimique et à des températures élevées.
Les équipements les plus courants dans les sites miniers où des revêtements renforcés de céramique sont utilisés sont les suivants :
- Goulottes de chargement et de déchargement
- Plaques d’usure pour bandes transporteuses
- Trémies
- Cyclones
- Plaques de distribution de l’alimentation des concasseurs à cône secondaires, tertiaires et quaternaires
- Alimentateur à bec pour broyeur à boulets
- Revêtements de tourillons et de spirales pour l’évacuation des broyeurs à boulets et des broyeurs semi-autogènes (SAG)
- Boîtes de jonction de décharge de broyeur
- Chambre de distribution des hydrocyclones, intérieurs, apex et canaux de décharge
- Barres transversales du crible vibrant, débordements
- Pompes à boues de décharge de broyeur à boulets ; raccords d’aspiration et de refoulement et internes
- Broyeurs verticaux
- Râteaux, cônes de décharge et coudes des épaississeurs de minerai et de résidus
- Pompes à résidus, tuyaux et coudes
- Planchers des cellules de flottation, trop-pleins et lavoirs
- Tambours d’agglomération, goulotte d’alimentation et coque
- Sections de tuyaux et coudes
- Corps de vanne, sièges et éléments d’étanchéité
- Réservoirs à lisier, agitateurs et sols
- Convoyeurs à vis et auges
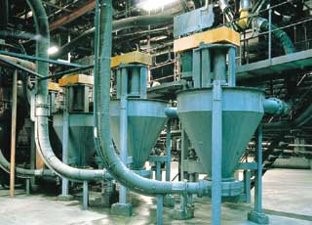
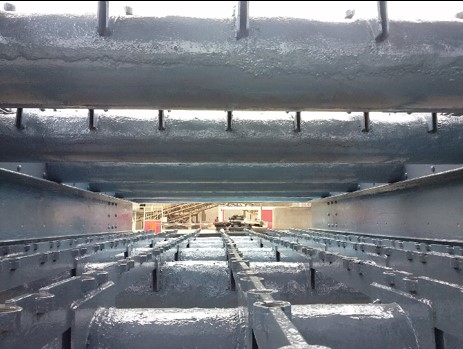
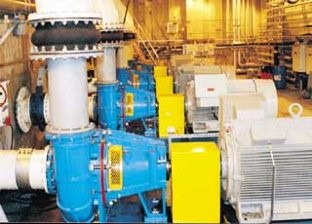
En conclusion, nous pouvons affirmer que l’utilisation de revêtements renforcés de céramique pour les équipements soumis à l’abrasion a eu un impact positif sur les pratiques de maintenance dans l’industrie minière et de traitement des minerais à travers le monde, grâce à la facilité d’utilisation, à la fiabilité, au bon rapport qualité-prix et aux performances de ces matériaux.
Avec le développement de nouvelles technologies, nous pouvons constater que la demande de ces types de revêtements ne fera qu’augmenter à l’avenir, et ce sont les besoins du marché qui décideront du type de revêtements à développer.
Parlez-en avec nous ! Nous nous ferons un plaisir de vous proposer la solution de revêtement optimale. N’hésitez pas à contacter notre Expert Desk pour de plus amples informations.
Vous pouvez également faire une première sélection à l’aide de notre sélecteur de produits. Nos conseillers produits se feront un plaisir de vous aider à choisir le produit idéal pour votre application.